
Blast Furnace Slag
Origin
In the production of iron, iron ore, iron scrap, and fluxes (limestone and/or dolomite) are charged into a blast furnace along with coke for fuel. The coke is combusted to produce carbon monoxide, which reduces the iron ore to a molten iron product. This molten iron
product can be cast into iron products, but is most often used as a feedstock for steel production.
Blast furnace slag is a nonmetallic co-product produced in the process. It consists primarily of silicates, aluminosilicates, and calcium-alumina-silicates. The molten slag, which absorbs much of the sulfur from the charge, comprises about 20 percent by mass of iron production. Figure below presents a general schematic, which depicts the blast furnace feedstocks and the production of blast furnace co-products (iron and slag).
Different forms of slag product are produced depending on the method used to cool the molten slag. These products include air-cooled blast furnace slag (ACBFS), expanded or foamed slag, pelletized slag, and granulated blast furnace slag.
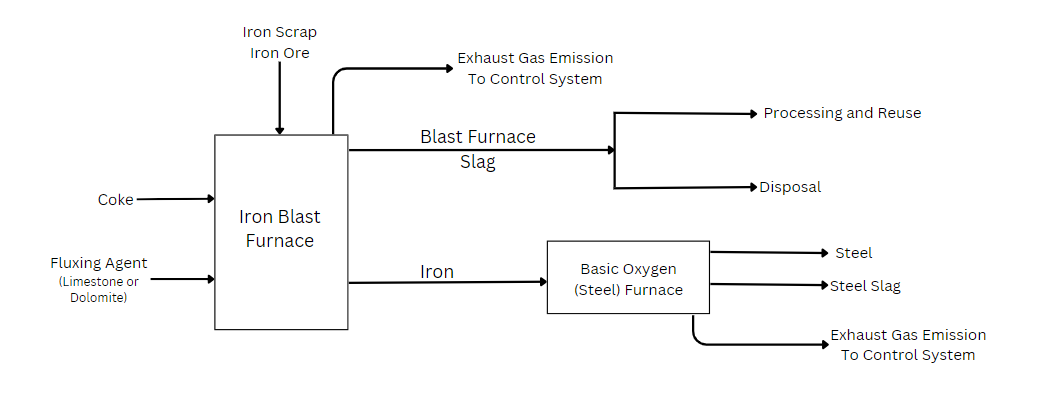
Expanded or Foamed Blast Furnace Slag
If the molten slag is cooled and solidified by adding controlled quantities of water, air, or steam, the process of cooling and solidification can be accelerated, increasing the cellular nature of the slag and producing a lightweight expanded or foamed product. Foamed slag is distinguishable from air-cooled blast furnace slag by its relatively high porosity and low bulk density.
Pelletized Blast Furnace Slag
If the molten slag is cooled and solidified with water and air quenched in a spinning drum, pellets, rather than a solid mass, can be produced. By controlling the process, the pellets can be made more crystalline, which is beneficial for aggregate use, or more vitrified (glassy), which is more desirable in cementitious applications. More rapid quenching results in greater vitrification and less crystallization.
Granulated Blast Furnace Slag
If the molten slag is cooled and solidified by rapid water quenching to a glassy state, little or no crystallization occurs. This process results in the formation of sand size (or frit-like) fragments, usually with some friable clinkerlike material. The physical structure and gradation of granulated slag depend on the chemical composition of the slag, its temperature at the time of quenching.
Air-Cooled Blast Furnace Slag
If the liquid slag is poured into beds and slowly cooled under ambient conditions, a crystalline structure is formed, and a hard, lump slag is produced, which can subsequently be crushed and screened.